Foreword
The quality of commissioning and ongoing maintenance of life safety systems is obviously of critical importance to how the system functions, not only at the time of handover to the developer, occupants or estate management company, but 5, 10 or 20 years time.
The commissioning stage is the final check of the installed system, this is the time when all checks must be thoroughly undertaken. It is at the time when any potential failures must be identified and corrected otherwise they will remain as a weak link in the performance of the system at the worst possible moment, in the event of a fire.
In the two previous documents we have published on smoke control system design, I have touched on the poor quality of design and installation that I have witnessed, much of which I would consider serious failures by supposedly competent organisations.
Having witnessed such poor practice, I have often wondered how such systems could possibly have been formally tested and commissioned, and how could anyone have witnessed the commissioning of such systems and accepted handover.
This report, prepared by members of my highly experienced team, highlights what any proficient smoke control company would/should/must do to guarantee as far as anyone can, a reliable system that will perform in accordance with the best practice in the industry in the event of fire.
The following report covers the process from submission of the design proposal to handover. I hope you find it of help.
David Royle
Managing Director
Validation of design
It is important to first establish the design objectives and strategy for the smoke control system and cross reference this with the overall fire strategy for the building. All this should be contained in the original technical submission prepared for the smoke control system.
The technical submission should include the following information and documents:
-
Detailed written description of the system, setting out the design objectives, strategy and performance criteria
-
All calculations to support the design
-
Clear specification for equipment used
-
Cause & effect chart ï‚· Layout drawings
-
Installation detail drawings
-
System schematics
-
CFD report if applicable
CFD modelling is commonly used to validate a system design prior to installation and can aid the understanding of how a system functions by both the designer and the regulatory bodies who will be responsible for approving the smoke control system’s installation. If a CFD model has been produced to validate the system design, it should be included in the technical submission pack.
It is also wise to include individual product compliance certificates confirming that the products used in the system have been tested to and are compliant with the relevant standards. Providing this information at technical submission stage this enable a quicker confirmation of approval by Building Control.
Documentation issued at the handover stage must also include a full operating and maintenance package in order to comply with Regulation 38, (see Building Regulations 2010 - Regulation 38 below)
Regulations & Standards
All smoke control systems should be designed and installed in accordance with the relevant regulations and standards, and compliance should be the first check in the commissioning process.
Building Regulations
Approved Document B deals with all aspects of fire protection in buildings, from the building’s construction to measures to assist escape, such as fire detection, smoke control and fire service access. There are three sections which are particularly relevant to smoke control systems:
B1 – Section 2 dealing with means of escape and smoke control systems serving them
B3 – Section 11 dealing with car park ventilation
B5 – Section 18 deals with venting of heat and smoke from basements
Approved Document F1 deals with the ventilation of enclosed car parks under day to day ventilation, giving guidance on natural and mechanical ventilation as well as limitations on pollution levels.
Building Regulations 2010 - Regulation 38
In order to comply with Regulation 38 of the building regulations, it is required that all fire safety information for new or altered buildings be passed to the responsible person as defined in the Article 3 of the Regulatory Reform (Fire Safety) Order 2005 on the completion of a building or on occupation, whichever comes sooner.
The information provided should contain full details of the smoke control system design to a level which will enable the ongoing maintenance and operation of the system serving the building.
No completion certificate should be handed over by the Building Control Officer without being satisfied that all the necessary documentation compliant with regulation 38 has been provided at handover.
BS7346: Part 8:2013
Code of Practice for planning, design, installation, commissioning and maintenance provides good guidance on commissioning.
BS 9999-2008
BSi describes BS 9999:2008 as being the fire safety code of practice for building design, management and use. It is based on government guidance and provides a best practice framework for fire safety and outlines ways to meet fire safety legislation through a more flexible approach to design.
BS9991-2015
BS 9991-2015 deals specifically with fire safety measures in residential buildings, specialised accommodation, though not residential care homes.
Guidance includes the design of new buildings, and to extensions and material changes of use to existing buildings.
It does not cover hotels, caravans/mobile homes, hospitals, residential care homes, places of lawful detention or hostels.
BS7346: Part 7: 2013
Components for smoke and heat control systems. Code of practice on functional recommendations and calculation methods for smoke and heat control systems for covered car parks
Commissioning of Car park Ventilation Systems
Guidance for the commissioning of a car park ventilation system is included in BS7346: Part 7: 2013 and the standard covers natural, assisted natural and mechanical ventilation systems, including ducted and jet fan systems. The standard includes a comprehensive checklist for commissioning.
This document focuses on the full mechanical systems and the following table identifies the key items that must be checked and verified.
Table 1 – Essential checks to be included in the commissioning of a car park ventilation system
​
​
​
​
​
​
​
​
​
​
​
​
​
​
​
​
​
​
​
​
​
​
​
​
​
​
​
​
​
​
​
​
​
​
​
​
​
​
​
Where items listed are not installed, e.g. CO monitoring system, mark not applicable (N/A).
Ducted systems are rarely installed nowadays but, where they are installed, measurement of the total airflow rate and checks on the distribution of airflow to ensure there are no obstruction to airflow resulting in stagnant areas are vitally important.
​
​
​
​
​
​
​
​
​
​
​
​
​
​
​
​
​
​
​
Commissioning of Smoke Control Systems Serving Residential Apartments
There are many types of application of smoke control systems as there are several types of system that may be applied to them, for example, natural ventilation, mechanical depressurization, pressurization and so on.
This section of the document will deal with smoke control systems serving residential apartments and commissioning of depressurization and pressurization systems. Much of what is outlined here will be equally relevant to other similar applications.
BS7346: Part 8:2013
Code of Practice for planning, design, installation, commissioning and maintenance provides good guidance on commissioning and maintenance of smoke control systems and states that “smoke control systems equipment should only be maintained by a competent person with specialist knowledge of smoke control systems”.
BS9991: 2015
Fire Safety in the design, management and use of residential buildings – Code of practice, proposes reference to BS7346: Part 6 for commissioning of smoke control systems serving residential buildings.
BS9999: 2017,
dealing principally with commercial buildings, makes reference to BSEN12101: Part 5: 2017 for the commissioning and handover of “smoke control systems employing pressure differential systems”.
As with the commissioning of any system, the starting point must be surveying the system to check that the installed system exactly reflects that which is detailed in the technical submission and drawings. Having confirmed this, then a detailed functional test can proceed.
​
​
​
​
​
​
​
​
​
​
​
​
​
​
​
​
​
​
​
​
​
The principal objective of any smoke control system will be to protect the primary escape routes, the most important of which is the stairwell. The stairwell will be the escape route used by all residents in the event of fire, particularly those residents located above the fire floor. Whilst all elements of the commissioning tests are important and must be thoroughly examined, particular attention should be paid 7 to verifying that the specified performance criteria is met in this area. Synthetic cold smoke tests can be very useful in visually demonstrating the performance of the smoke control system.
Table 2 – Essential checks to be included for each level in the commissioning of a smoke control system
System Handover
Regulatory Reform (Fire Safety) Order 2005
The Regulatory Reform (Fire Safety) Order (RRO) was introduced in October 2006. The document is aimed at helping regulatory authorities and public bodies to better understand their responsibilities and the intent of specific aspects of the order.
Importantly, this guidance details appointment of and the requirements imposed on the “responsible person” as defined under the order. It also covers arrangements for enforcement of the Order.
Installation and Operating Data
The material included in the handover documentation should provide sufficient information to enable any competent person to operate and maintain the system.
The full technical submission detailing the operation of the installed smoke ventilation scheme should be included in the documents handed over at the completion of the commissioning of the system. The technical submission should include all the items listed above under Validation of design and “as installed” drawings and schematics.
In addition, full details of the applicable operating and maintenance requirements for the system and all equipment and components included in it.
Test certificates
Test certificates for all equipment should be included in the handover documentation, included the Commissioning Certificate verifying that the system has been tested and found compliant with the relevant regulations and standards.
Additional certificates should also include individual compliance certificates for individual components such as fans, dampers, ventilators and fire detection system.
The handover documentation should also include the name of the “Responsible Person” identified to the representative of the system installer, and their contact details. If this information is unknown at the time of the handover, this should be noted on the documentation and the name and contact details of the person responsible for witnessing the commissioning or accepting the handover of the system recorded in the documents.
​
​
​
​
​
​
​
​
​
​
​
​
​
​
​
​
​
​
​
​
Maintenance of smoke control systems
Only when all components within a smoke control system are functioning correctly and reliably, is a smoke control system viable.
BS9999 sets out guidance for the regular examination and testing of fire safety systems Advanced Smoke Group endorses this guidance in its own service and maintenance policy, advising that the following program is adopted as the basis of a planned maintenance program.
Daily
The smoke control system should be inspected daily, so that it can be confirmed that:
a) The control panel indicates normal operation or, if any fault is indicated, that it has been logged and the appropriate action taken
b) Any fault recorded the previous day has received attention and been rectified.
Weekly
Activation of the smoke control system should be simulated once a week. It should be ensured that any fans and powered exhaust ventilators operate correctly, smoke dampers operate, natural exhaust ventilators open, automatic smoke curtains move into position, etc.
NOTE: On large multi-zone installations it might be acceptable, with agreement from the relevant authorities, to rotate the equipment tested so that a system is tested every week and individual items are operated at intervals of no more than three months.
Three Monthly
In addition to the above checks, the actuation of all smoke control systems should be simulated once every three months. All zones should be separately tested and it should be ensured that automatically opening ventilators (AOV’s) operate and dampers function correctly and, in the case of mechanical systems, fans operate reliably.
Six Monthly
Smoke control systems, and all controls and components within it, should be inspected and tested by competent persons every six months and certificates confirming the functional integrity of the system.
Annually
In addition to all checks undertaken in the six monthly procedure, a full commissioning check should be undertaken.
For mechanical systems, the airflow performance of the extract or pressurisation fans should be checked as well as the air velocity across door openings.
For car park jet fan ventilation systems, as well as the extract rate being measured at the extract points, the operation of the jet fans should be checked and, for zoned systems, confirm activation of the system according to the zone in which a fire signal; has been activated.
Where carbon monoxide detection is installed in car parks, the calibration of the detector heads should be checked and adjusted where necessary.
Certificates confirming the functional integrity of the system and its compliance with the original performance criteria should be issued.
General
A log should be kept of all any faults detected, remedial action taken and of any components replaced.
For definitions and responsibilities with regard to fire safety, reference should be made to the Regulatory Reform (Fire Safety) Order (RRFSO) – which clarifies them and who responsible and competent people might be.​​​​​​​​​​​​​​​​​​​​​​


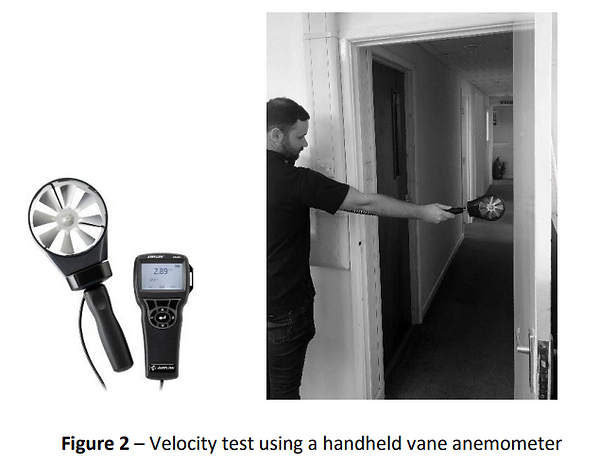


